PEEK is a Polyetheretherketone, and it belongs to the Superpolymers category.
The PEEK is a thermoplastic aromatic polymer.
It is semycrystalline polymer.
The melting temperature is around 343 °C and for this reason it has been processed between 380 – 420 °C. The extruder temperature profile depends on the extruder size, screw profile, screw rpm, line speed, etc.
PEEK, unlike fluoropolymers, can be processed by conventional equipment.
The extruder barrel and screw can be made in nitrated steel without using bimetallic barrel or hastelloy screw.
The crosshead is in hardned steel and not in Hastelloy.
GENERAL PROCESSING
The PEEK is supplied in granules.
The granules supplied are normally already dried. PEEK can absorb humidity once the bag is opened.
In order to get the highest quality of the extruded it is better keeping the humidity content lower than 0,02% by using hot air circulation oven.
The granules can be drier for 3 hours at 150°C.
Due to the fact that PEEK is semicrystallin polimer, the properties of the insulation depend on the re-crystallization process after the crosshead that acts on the dimensions and distributions of the crystals.
For a correct re-crystallization process of the insulation, the cable/covered wire must be cooled down by air for at least 4-8 meters after the crosshead. Of course the air cooling lenght depends on the insulation tickness and line speed.
The PEEK can be cooled down by water after the air cooling.
So, as soon as the re-crystallization process is terminated the cooling water (even hot water) can be used.
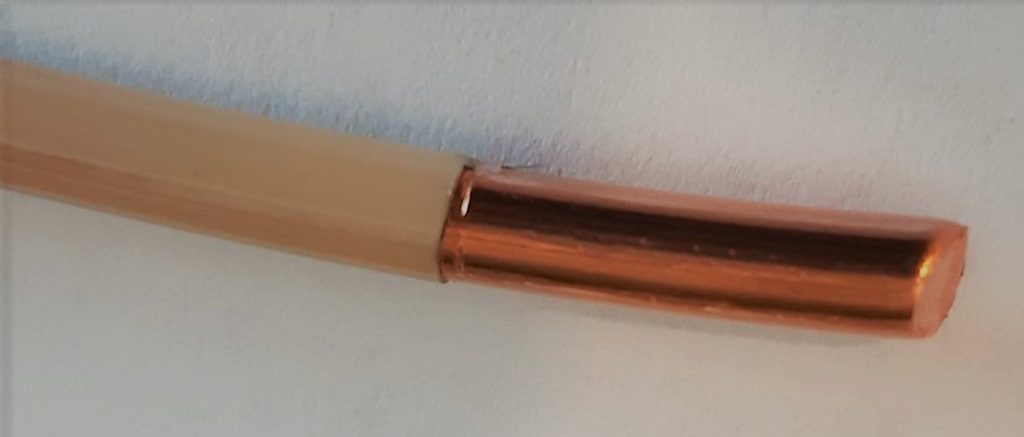
In case of using water, immediately after the crosshead, the cable surface can get some defects such as roughness, cracking, etc.
The wire to be insulated should be pre-heated before insulation. The wire or cable can be preheated between 120-190°C. The temperature could change in according with the wire dimension and line speed.
The pre-heating process even increases the plastic adhesion on the conductor/wire.
EXTRUSION CROSS HEAD
The extrusion head is made of hardened steel and not in Hastelloy. Of course hastelloy equipments could be used.
The distributor must have a correct conicity in order to:
- Easy extraction and no risk of distributor blocking
- Lower shear rate and low entrance speed
- Higher insulation or jacketing concentricity
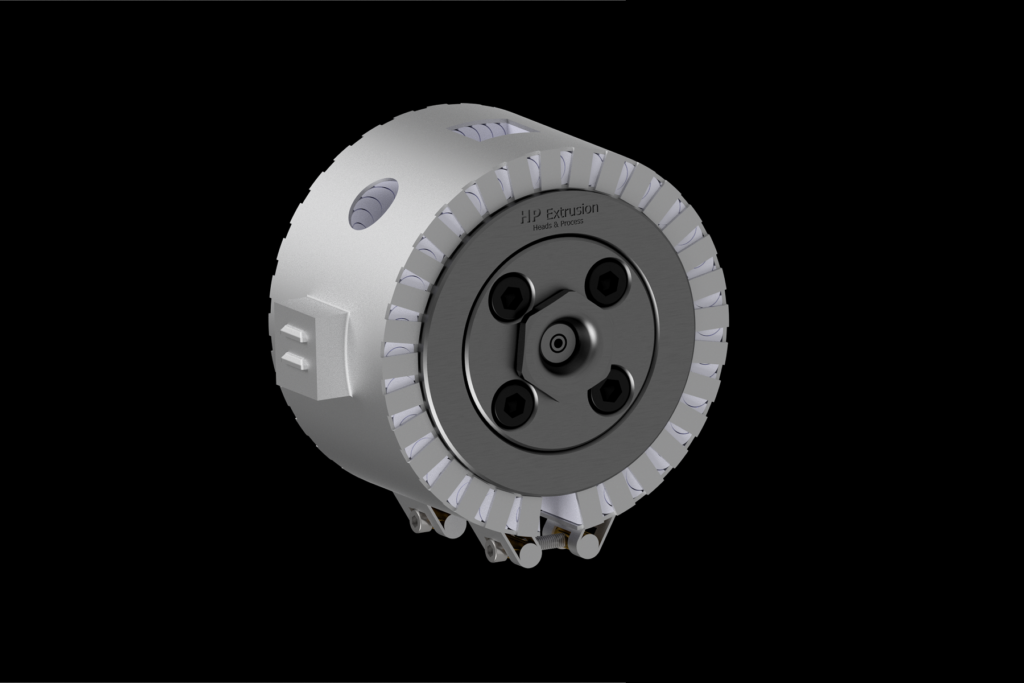
The leakage zone of the distributor, as well as the flowing passage into the head, must be properly calculated and designed in order to avoid material stagnation, material burning.
The flow pattern has to be not so long and properly calculated.
TOOLS
Pressure – Semipressure tools or tube tools can be used.
For tube tools: 2< *DDR < 6 and 1,01< *DRB < 1,05.
The values are indicative because they depend on many factors such as:
- Thickness of compound
- Type of compound used
- Line speed
- Die temperature and extruder temperature profile.
- Extruder screw rpm, etc.
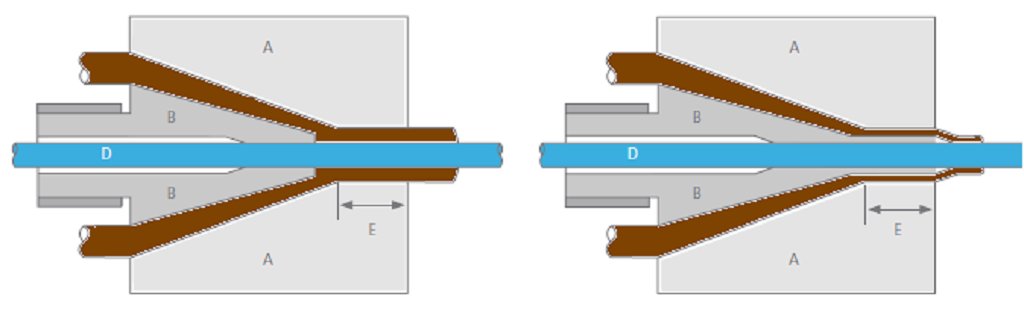
By using pressure tools, the die can be realized with:
- one angle and final Cylindrical land (Semi-pressure)
- two angles and short land. (Pressure)
CLEANING PROCEDURE
The PEEK can be left inside the extruder in case of stopping, but keeping the extruder temperature less than 340 °C.
In order to clean the extruder and crosshead, after the production with PEEK, many methods can be applied, but for all of them the procedure must be carried out in hot condition:
Using Cleaning Material. The PEEK must be removed from the extruder hopper. Fill the hopper with cleaning compound and extrude it at low screw rpm. Wait till the cleaning compound gets out from the head. When the cleaning material doesn’t contain peek, stop the feeding and wait till the extruder get empty.
As soon as the extruder is empty the manual cleaning of the components can start.
The cleaning procedure must be carried out using brass brushes or brass tools only.
It is forbidden to use steel tools or steel brushes, they could damage the surface of the head components, screw, etc.
Tip and die are the first parts to be cleaned. First of all, unscrew the die nut and pull out the die. Clean it till it is still hot. Than extract the tip by means the tip extractor and clean it till it is hot.
Then extract the flow distributor and clean it manually by brass tools, brass brushes and compressed air.
Then clean the inner head-body. As soon as the the head has been cleaned, go on with extrusion screw and barrel cleaning.
Using Fluorinated or partially fluorinated material. “The permanence of the fluoropolymer into the extruder and cross head must be as short as possible due to the fact that the equipment is not in Hastelloy”.
Unload PEEK from extruder hopper. Feed the extruder with FEP (just few kilos). Keeping the same temperature profile, switch the extruder on (between 5-10 rpm).
Wait till FEP gets out from the head (from tools). Then stop the FEP feeding and unload the FEP from hopper. Let the extruder turns till it gets empty.
Once the extruder is empty it is possible to dis-assembly the components to be cleaned as below described.
First of all, remove the tools from the head and clean them by compressed air and brass brushes.
Then dis-assembly the flow distributor and clean it till it is hot by compressed air and brass brushes/Tools.
As soon as the extrusion head has been cleaned it is possible to switch off its thermoregulation.
Use silicon spray to protect the head and its components once cleaned.
The next step is to clean the extruder screw and barrel.
For Extruder cleaning the thermoregulation must be kept on.
Open the extruder clamp, clean the breaker plate (or opened ring). Then extract the screw step by step for cleaning. The screw must be kept inside the hot barrel and only the part of the screw to be cleaned must be pulled out from it. Once part of the screw out from the barrel is cleaned, the next part of the screw to be cleaned can be pulled out from the barrel.
As soon as all screw has been pulled out from the barrel and cleaned, the barrel must be cleaned. In order to clean properly the extruder, barrel its thermoregulation must be kept on.
For barrel cleaning, brass or copper brush can be used. The brush should have the same barrel inner diameter or lightly bigger.
If no brushes are available, it is possible to use a home-made brush.
It can be build using a piece of wood or a common broomstick, longer than the barrel.
Cover the broomstick with clothes or rags in order to get approximately the same diameter of the barrel. Wind the bunched copper wire around the rags or clothes and fix it.
Then insert it into the barrel and clean it manually. The copper wire will clean the barrel like a brush, without damaging the inner barrel surface.
To push out of the barrel parts of compound, powder compressed air can be used.
Once the extruder barrel is cleaned switch off the extruder thermoregulation and cool it.