SILICONE and RUBBER HEAD
HP-SIL and HP-TH series are cooled/thermoregulated crossheads totally made by high quality of hardened stainless steel, designed for silicone and rubber.
HP-Sil and HP-TH can be single layer heads or dual layer heads for Skin/Stripe.
The head is realized with thermal treatment plus special coating in order to guarantees the highest material smoothness for lowest friction, No compound overheating due to the mechanical friction, no material stagnation as well as wear and oxidation resistance.
The head is compact for lowest residence time.
The head has been designed with efficient cooling and thermoregulation circuit, avoiding material stagnation, avoiding material overheating.
They are properly dimensioned in terms of conicity and nominal diameter of the distributors and inner head body, feeding channels, distribution channels, barrier section and flow paths, assuring high production efficiency and excellent concentricity.
The perfect and efficient cooling/thermoregulation circuit assures an excellent thermal distribution.
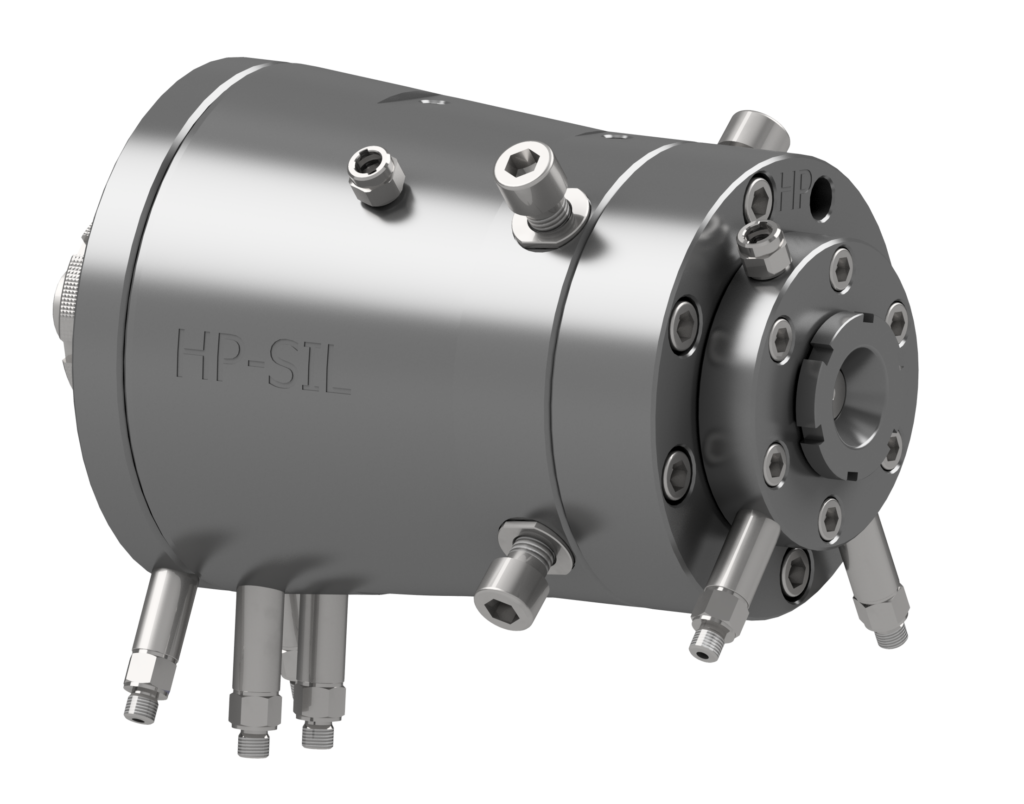
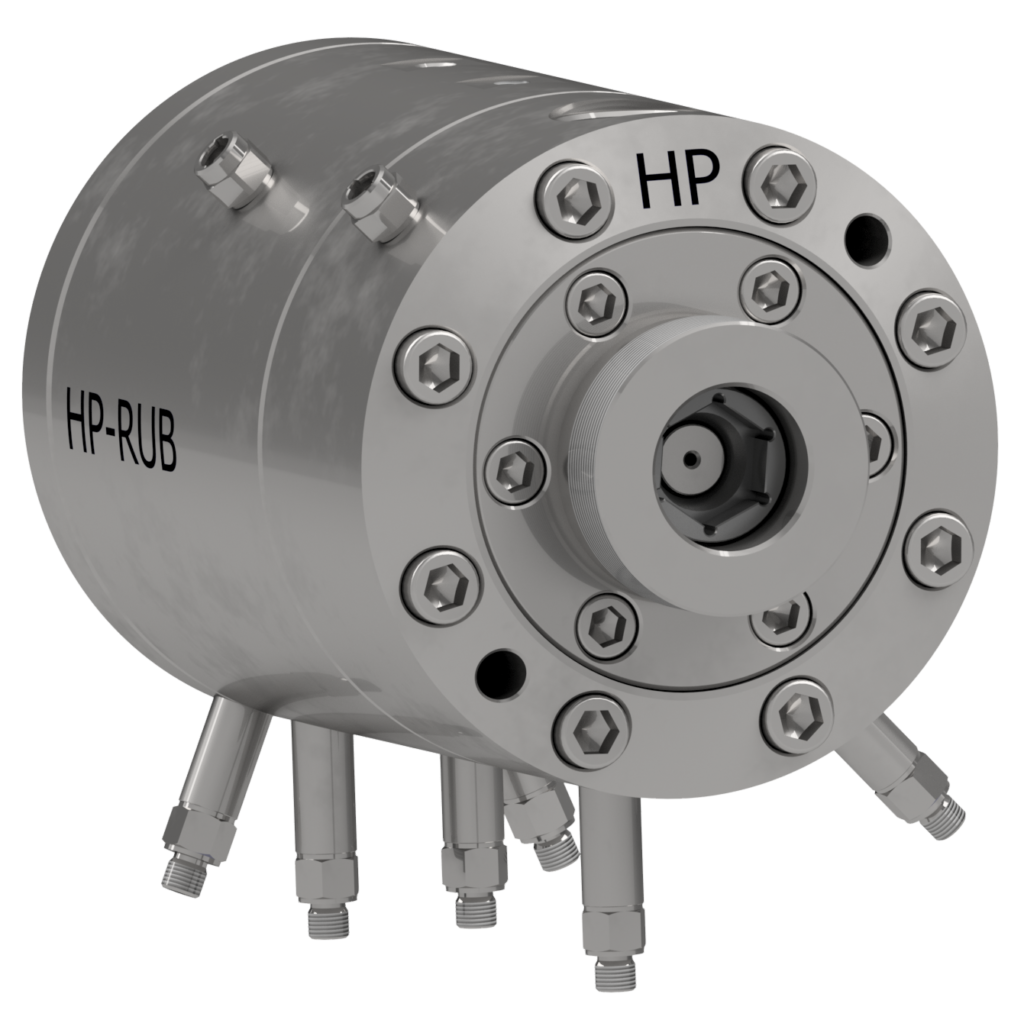
The melt flow distributor as well as every flow sections are subjected to new generation treatments in order to achieve high micro-hardness up to 3000 HV for high wear resistance, higher Abrasion resistance and highest material fluidity.
The melt flow distributor can be cooled/Heated by dedicated liquid circulation in order to control and stabilize the temperature of the inner substrate.
The distance between tip and die can be regulated by axial die movement and axial tip holder movement.
The tip holder, flow distributor are perfectly and accurately polished with proper strict tolerances reducing ovalizations and the strokes within microns. Moreover they are subjected to additional new generation treatments to increase the surface hardness and reducing the static and dynamic coefficient of friction between compound and flow channels.
This allows an easiest movement of the tip holder as well as distributor extraction without using LEVERS that could be dangerous for the operators safety.
The rings for single layer or skin/stripe are properly cooled/heated and placed into the front head body for compactness of the head. The rings can be easily and quickly assembled and dis-assembled and without removing the front head. The rings are properly designed for excellent flow distribution and skin thickness distribution.
The perfect design of the flow distributors and of the flow sections, assure:
- Higher smoothness and higher material fluidity
- Reduced extruder pressure and no material overheating
- Lower residence time
- No material stagnation
- Lower Material over-heating due to lower friction between silicone and head components.
- Lower internal friction among macromolecules, reducing the internal auto-heating of the silicone.
- Easier assembling/dis-assembling
HP-SIL has an optimized shape and cooling system in order to guarantee the highest cooling efficiency and perfect material distribution for excellent concentricity with lowest residence time.
PROCESS MODE
The head can work in:
- Single layer
- Dual layer (Single layer + Skin/Stripes)
CENTERING
The head are available with different centering system.
- Fixed centering
- Manual centering from front with fast tools change
- Manual centering from rear (Optional)
GUM SPACE
The gum space can be regulated by:
- Axial die movement from front
- Axial tip holder movement from rear.
The design, proper and strict tolerances and treatments allow an easy and light movement of the tip holder without locking and without using lever that can be dangerous for the operator safety.
COMPOUNDS PROCESSED
SILICONE, RUBBERS
COOLING or THERMOREGULATION
The head is cooled or thermoregulated by liquid circulation.
The cooling circuit can be easily cleaned any time it is required.
- Tip Holder movement from rear for gum space regulation
- Fine centring system from rear “Fine-Adjustment system”
- Head support and trolley
- Telescopic system for distributor support
- Special melt flow distributors with inner liquid circuit
- Vacuum connector
- Connecting flanges
- Extruder clamp/jaw
- Breaker plates
- By-pass
- Special treatments and coatings for wear and abrasion resistances
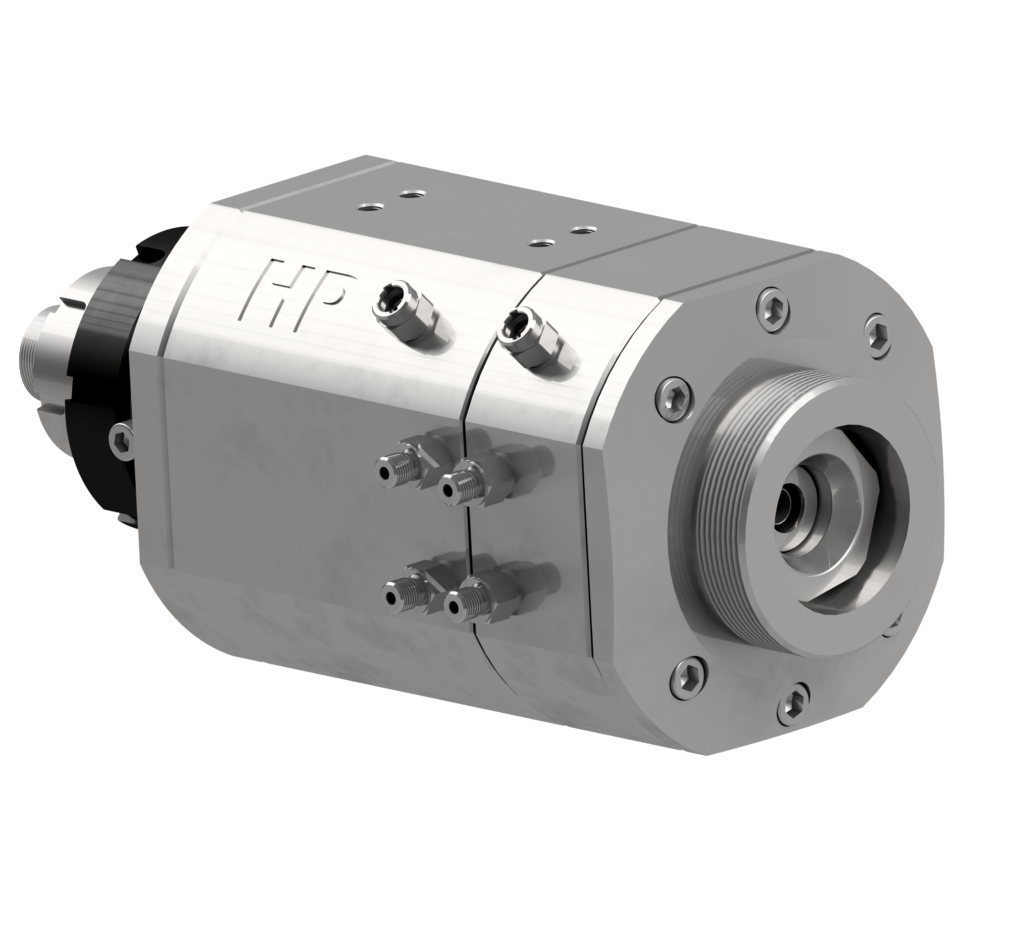