The extruder and cross head are the most important components that constitute the extrusion line.
Regarding the extruder, very important is the design of the screw and barrel and thermoregulation system. Let us remember that the screw profile, its compression rate and screw rpm acts on the visco-elasticity of the compound processed which enters into the head. The viscosity of the compounds entering into the flow distributor act on the back pressure value and on the cable quality.
Even the extrusion head is an important factor the design and dimensioning of the flow distributor, distribution and pumping channels, distributor conicity, distributor diameter at the material entrance, gap of the leakage zone, in according with the correct design of the flow chamber and tools chamber.
Regarding the extruder and cross heads an important role is played by:
- Design and dimensioning of the extrusion screw, extrusion barrel and extrusion head.
- Type of the material used
- Thermal Treatment and additional surface treatment
- Tolerances on the single components as well as thermal dilation calculation.
In order to understand the importance of the materials and treatments in addition to the their calculation we analyze the drag flow effect into the extruder. This concept is partially applicable on the extrusion head design.
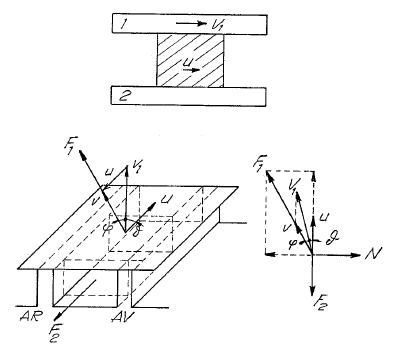
F1 = f1*S*p
where F1 is the driving torque exerted by the barrel in the same direction as v1 (equivalent linear speed of the barrel);
F2 = f2*S*p
where F2 is the resistant force exerted by the barrel in the opposite direction to v1.
P is the pressure that compresses the solid bed of pellets (or powder).
S1 ed S2 sono le superfici di contatto che idealmente, nel modello dei piani paralleli, sono supposte uguali.
f1 ed f2 are the contact surfaces, which are assumed to be ideally equal as per the Plane- parallel model.
For the material to be fed, f1 must be f1 > f2
In reality, it is possible to demonstrate that solids are fed even if f1 = f2. To explain this we must make reference to real elicoidal geometry. Without going into the detailed calculation it is apparent that the surfaces S1 and S2 are not identical and the lever arms with which the friction forces are applied are also different. Solid bed progression therefore becomes:
f2/f1(D2/D1)2 < cosθ
From which we can deduce that even if f1 = f2 the solid can be fed . Also the smaller the D2/D1 ratio the greater feed efficiency will be. If f1< f2 .material will adhere to the screw and rotate with it; consequently it will not be fed.
Clearly, it is desirable to reduce the screw friction coefficient and increase the barrel friction coefficient. Hence grooves, which are parallel to the screw axis (although other forms do exist), are realized within the barrel to supercharge the final metering zone and enhance melt output.
Of course in order to reduce the friction coefficient is possible to realize different treatments such as Chrome plating (Chrome flash after ionic nitration) or other superficial treatments.

Extruder and cross head have a processual bi-univocal relation and due to this it is possible to associate the extruder screw to the flow distributor and barrel to the head body.
As per the screw, even for the flow distributor is important to reduce the friction coefficient between compound and flow channels. Considering the fact that the driving force is generated from the screw is even important reduce the friction coefficient between compound and inner head body.
In order to reduce the friction coefficient is possible to act on the mechanical machining (finishing, polishing) and on the surface treatment as well.
The surface treatments must guarantee an higher micro-hardness even to face to the high viscosity of the compound on the market and mainly for HFFR, LS0H, XLPE FR, XL LS0H, loaded PVC, fillers, etc.
The treatments can be:
- Thermal treatment to improve the surface hardening such as Nitration, tempering, cementation.
- Single or multi Surface treatments in order to increase the micro-hardened and reducing the mechanical friction.
According to the type of treatments the material must be correctly chosen.
The surface treatments can be:
- Chrome plating
- PVD (CrN, TiN, DLC, etc).
- Disulphide o TRIBO-W, etc., normally used to reduce more the friction between mechanical components (flow distributor, By pass valve, breaker plate, etc.).
The cross head and all their components must be designed choosing the proper material and proper treatment.
The thermal and surface treatments must be associated with correct geometrical and dimensional tolerances and with correct distributor, ring, by-pass, tip holder design, in order to guarantee:
- Wear resistance
- Reducing of the extruder back pressure
- Reducing the localized material over-heating
- Easy flow distributor extraction, only if associated with proper flow distributor calculation in terms of angle (conicity), diameter and thermal dilatation calculation.
- Easy movement and no gripping or blocking.
- Easy by-pass valve movement and no seizure or blocking.
HP Extrusion guarantees an highest product quality, high material quality used for head and components construction. This associated with proper treatments will guarantee the correct heads and components functionality as well as the wear resistance and production performance.
The quality of our products give advantages :
- Operational: Repeatability, easy assembling, easier dis-assembling and set up from operator side.
- Processual: higher smoothness for better material flowing, reduction of the localized material over-heating due to the friction between compound and distributor, no material stagnation, higher cable concentricity, high cable quality and lower extruder back pressure.
- Mechanical: higher micro-hardened, higher wear resistance and lower friction coefficient between each single component. In according with more and more strict tolerance we will avoid the blocking or gripping effect even during relating movements (By-pass valve, Tip holder, etc.)