The XLPE for cable insulation can follows different process:
- Monosil
- Sioplas
- Visico®
In this section we will deal with XLPE Monosil.
Cable insulation in XLPE by monosil process (liquid silane) allows to produce the cable in according with all needs and requirement or specification to be respected. This advantage is due to the possibility to choose and dose each single component of the compound.
Extruder Dosing
The extruder used is normally 26<L/D< 32, longer than standard extruder, in order to guarantee a good mixing and homogenisation of the compound. Standard extruder 24<L/D<26 could be used if a proper pre-mixing has been done before feeding the extruder.
The extruder must be fed with different elements, such as:
- LDPE, LLDPE;
- Antioxidant, in case of
Aluminium, Almelec insulation, etc. - Carbon Black or other
master-batches; - Flame retardant moisture;
- Additives for silane
absorption; - Liquid silane.
The dosing should be realized by means of gravimetric dosing system, even if silane could be even injected by volumetric pump correctly calibrated and synchronized with extruder rpm.
LLDPE and Carbon Black granules must be dried or dehumidified for at least 3-4 ours at 60-70 °C, before using them. Higher is the temperature of the LLDPE into the extruder feeding zone and higher is the silane absorption.
The dosing in terms of percentage of each element could change in according with equipments, screw design, cable to be produced, hot set test, shrinkage, etc. The typical dosing can be:
- Liquid silane: 0,90-1,80 %. It depends on type
of silane used, Hot set test value, cable characteristics, etc.; - Antioxidant: 0,6-1,3%;
- Carbon black: 1 – 8 %;
- Additives for Silane absorption: 5 -10 %.
Carbon black is important for UV resistance and for silane absorption as well.
An important function is played by the mixing system used. The good premixing, proper moisture
homogenization and performant screw design assure a constant and stable cable property even during the acceleration and deceleration of the line.
The liquid silane must be protected from air, humidity by means of nitrogen.
The nitrogen will avoid the silane crystallization into injection device, pump or flowing pipes.
The nitrogen pressure into the silane barrel is normally less than 0,8 bar. Pressure higher than 1,5 bar can deform the barrel.
The Humidity protection filter could be used if nitrogen connection is not available.
Liquid Silane Drum Safety-Storage and Quality
The silane drum usually has two different connection holes; one for silane pump and the other could be used for the nitrogen connection or anti-humidity filter.
If nitrogen flow is used in the drum to protect the silane, is important to know that the mechanical drum limit is 2-2,5 bar (Breaking test).
The correct storage, in terms of local temperature and humidity percentage, can act on:
- Silane quality in the drum;
- Silane drum safety.
“Quality Effect”:
The liquid silane is trimethoxi or triethoxi and it contains peroxide;
The peroxides present in the product will degrade with time even at low temperatures (30 °C). The shelf life the silane producers place on the products reflects ideal standard storage conditions, so below 30°C.
The lack of peroxide or its degradation is accelerated if storage temperature increases.
The Lack of peroxide reduces the silane reactivity.
“Safety Effect”:
The liquid silane and consequently the silane drum should be kept below 55°C and usually below the flash point temperature defined on silane data sheet you’re used.
At temperatures above 55°C the decomposition of the peroxide generates enough heat to self-accelerate the decomposition to the point of fire or explosion. The product MUST NOT be stored above 55°C NOT must be stored in direct sunlight.
The drum surfaces can easily reach temperatures above 55°C in direct sunlight condition even if ambient temperature is only 40°C.
Peroxide explosions can be extremely powerful. From a safety perspective only, the smaller the container the higher temperatures it can sustain before reaching the point of fire or explosion.
“Conclusion”:
The silane drum safety storage temperature must be below 25-40 °C (30 °C is the optimal storage temperature in terms of the product quality and its life time).
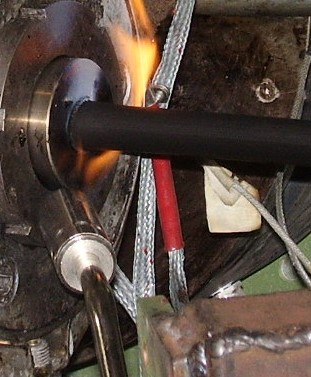
PRODUCTION ADVICING
Before starting with monosil XLPE production, all equipments must be cleaned.
After silane circulation, all parts must be cleaned by means of Ethyl alcohol (C2H5-OH) or in extreme cases (for example when crystallized silane is in connection pipes, silane pump,
injector, is noted) by acetone.
To start the production:
- Set the proper temperature profile into the extruder and cross-head;
- Switch on the screw thermostatization;
- Feed the extruder with LLDPE only and start the extruder at purging speed (3-8 rpm).
As soon as the LLDPE is getting out from by-pass or cross head, feed the extruder with all other
additives and at the end with liquid silane.
- Do not stop the extruder with liquid silane into the barrel.
- The minimum extruder screw rpm, in case of silane dosing, must not be lower than 8-15 rpm. If the extruder must be stopped first of all the silane dosing must be disabled and the barrel must be without silane.
- Do not switch off the thermostatization screw device if the liquid silane is into the barrel
If the screw thermostatization is off:
- XLPE can easily sticks on the screw surface
- The extruder can pump
The screw temperature should be set between 65 – 80 °C.
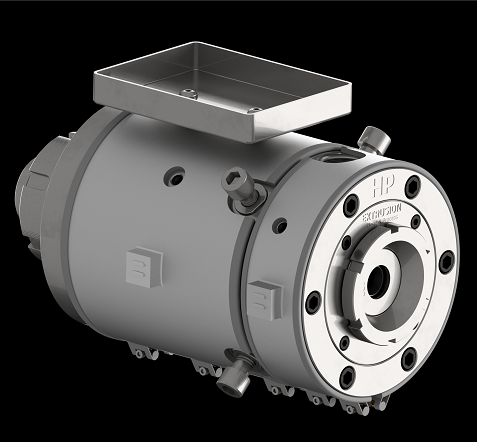

HEAD AND TOOLS
In case of using Semi-tube tools the vacuum pump must be switched on.
1,40< DDR<,1,90
0,97<DRB<1,02;
Elongation= [(Sf-S0)/S0]*100.
S0=л*(D2-C2)/4
Sf= л*(E2-A2)/4
DDR = (D2 – C2)/(E2 – A2) = S0/Sf
DRB = (D x A)/(E x C)
D= {[DDRx(E2-A2)]/[1-(A/(DRBxE))2]}½
D = (DRBxCxE)/A
Of course semi-compression tools can be used.
For Almelec (aluminum as well) is better to use the tube tools to avoid creating powder on the tools, reducing the plastic adhesion.
Flame (by burner) around the die can be used in order to:
- Remove the die drool;
- Get shiner and more brilliant cable surface.
The cooling trough must have 1 or 2 thermoregulated section with hot water temperature between 60 – 75
°C.